Investigation of residual stresses in additive manufactured superalloys used in industrial gas turbines by Neutron Diffraction
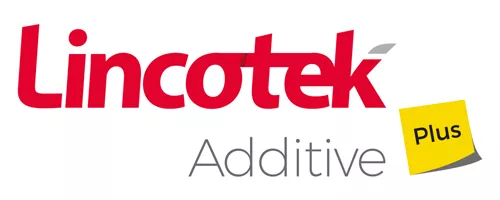
Lincotek is a global contract manufacturer providing special services in markets including industrial gas turbines, aviation, medical and other industrial fields since 1973. The company has championed innovation in additive manufacturing solutions since 2006 being at the forefront of research, design, engineering and manufacturing, and today with Additive Plus, Lincotek is able to simplify the supply chain, offering a complete additive service offer and taking responsibility for a whole range of processes in-house with the guarantee of a unique serial production expertise.
In Lincotek Additive, Nickel based superalloy parts are manufactured by selective laser melting (SLM) for industrial gas turbine (IGT) applications. When a metal part is 3D printed, one cannot just extract it from the machine and use it. The sample needs to be post-processed before it is ready to be used. Post-processing of parts such as thermal heat treatments is fundamental and truly challenging. It is this capability that sets Lincotek apart. Lincotek offers expertise in materials and superalloy development as well as in characterization.
The applied material analytics of ANAXAM using Neutron Diffraction helps Lincotek Additive to analyze the residual stresses of Nickel based superalloys after the printing process and after additional post-SLM heat treatments. Since the SLM printing process is directional and the cooling rates during the printing process are very high, residual stresses in the printed parts are present which limit the applicability of the samples in the “as-built” state. A thermal heat treatment is often applied after the SLM process to release the stresses but at the same time the microstructures can be altered. Therefore, a thorough understanding about the impact of SLM process and heat treatment parameters to the microstructural and residual stresses evolution will be essential.
Lincotek Additive can transfer the results obtained by ANAXAM directly to the SLM process optimization and heat treatment designs to further improve the additive manufactured parts.
For this customer project, ANAXAM used POLDI beamline at the Paul Scherrer Institute.
By using the advanced analytics of ANAXAM, Lincotek Additive gets a deeper insight and understanding about SLM-processed high temperature materials.”
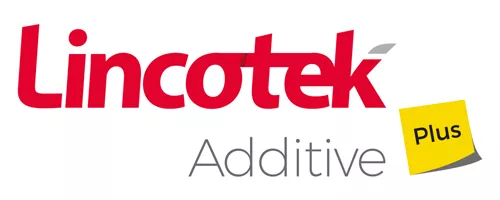